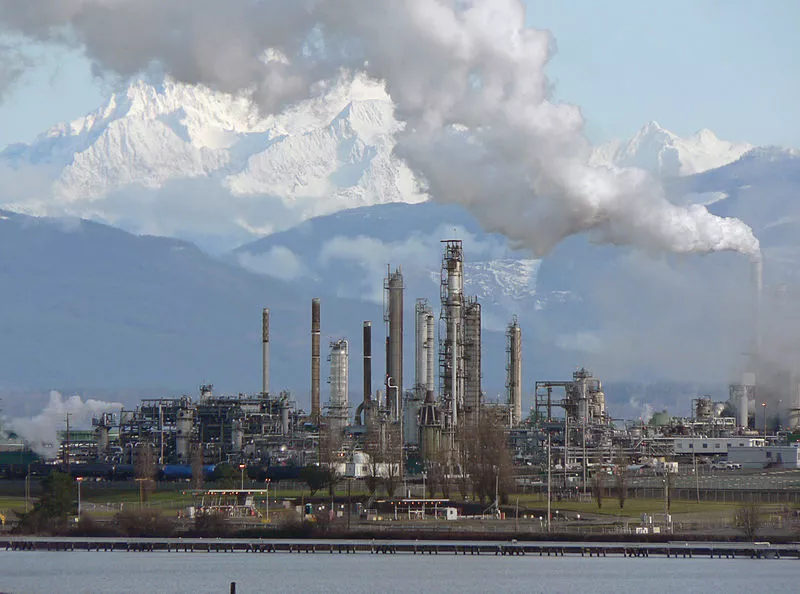
Last October we saw the State of California implement its "PSM for Refineries" standard and now the State of Washington's Division of Occupational Safety and Health (DOSH) appears to be following suit, releasing draft language to adopt a rule of its own. This new chapter will only apply to Process Safety Management (PSM) for petrochemical refining facilities.
This Washington PSM rulemaking is in the early stages, and the draft being sent to stakeholders is meant to serve as a discussion draft. The stated primary intent of this revised rule is to achieve the best occupational health outcome possible in regards to the refining industry. DOSH encourages stakeholders to review the draft language and share ideas that they may have to assist the project in moving forward.
Refineries that have had to implement the newly revised California PSM rules in that state know first-hand how challenging the interpretation and implementation of these rules can be. While the core elements of the final California regulations and the draft Washington regulations are described below, significant challenges can be presented to determine what is covered, what is a “Major Change” and what constitutes a “Major Incident,” to name just a few. Also, identifying and training employees to meet the new requirements such as DMRs, HCAs, and Human Factors could require significant resources.
Upcoming Key Dates and Input Opportunities: DOSH will review the language and take comments from stakeholders throughout the rulemaking process. The next meeting dates are:
- February 7, 2018 Time: 1:00 p.m.
- February 21, 2018 Time: 9:00 a.m.
There will be several other meeting opportunities as the process moves forward. DOSH will share those future dates when finalized.
Refineries in Washington should make the most of this opportunity and engage early in the rulemaking process to provide input on the proposed new obligations, language and timing in the draft. Moreover, companies operating outside of Washington and California should be concerned with the potential for these types of regulations to spread farther to other states. These regulations may overlap and potentially conflict with federal PSM and Risk Management Plan (RMP) regulations.
Core Elements of the Draft Regulations: The draft closely mirrors the revisions recently adopted by California. Some significant, proposed new requirements include:
- Damage Mechanism Reviews (DMR) – assessments of potential damage mechanisms that can affect process equipment, including corrosion, stress cracks and other material degradation. DMRs must be conducted for all processes within five years and as part of Major Changes, Incident Investigations and Process Hazards Analysis (PHA).
- Employee Representative – union representative, where a union exists, or an employee-designated representative in the absence of a union that is on-site and qualified for the task. The term is to be construed broadly, and may include the local union, the international union, or a refinery or contract employee designated by these parties, such as the safety and health committee representative at the site.
- Hierarchy of Hazard Controls Analysis (HCA) – assessing hazard prevention and control measures in priority order to eliminate or minimize a hazard with inherent control measures ranked more effective than passive, active and procedural measures.
- Human Factors – the employer must develop an effective human factors program to identify human factors-related issues such as staffing levels, fatigue, and interface with equipment and communication systems.
- Implementation – provides timing requirements for implementation of corrective actions from a PHA, SPA, DMR, HCA, Compliance Audit and Incident Investigation. It also addresses criteria for the employer to reject a team recommendation (a determination of infeasibility cannot be based solely on cost) and to change a team recommendation (must be an equivalent or higher order of inherent safety).
- Major Change – introduction of a new process, new process equipment or any new highly hazardous material; change outside safe operating limits; or any alteration that introduces a new process safety hazard or worsens an existing process safety hazard. Prior to implementing a major change, the employer must review or conduct a DMR and perform a HCA.
- Major Incident – an event within or affecting a process that causes a fire, explosion or release of a highly hazardous material and that has the potential to result in death or serious physical harm. Major Incident Investigations must include a person with expertise in determining root causes, provide for employee collaboration, be initiated within 48 hours and completed within 90 days, and review DMRs, PHAs, Safeguard Protection Analyses (SPAs) and HCAs. Each corrective action must be completed within 18 months.
- Management of Organizational Change (MOOC) – an assessment prior to the reduction of staffing levels, reduction of classification levels or increase in employee responsibilities and must be certified by the refinery manager and must provide for employee collaboration.
- Process – Any activity involving a highly hazardous chemical (a substance possessing toxic, reactive, flammable or explosive properties). The definition includes interconnected vessels, including separate vessels which are located such that they could be involved in a release.
- Process Safety Culture Assessment – a method to objectively define process safety values and beliefs and evaluates hazard reporting and response, safety incentive programs and priority of process safety during upset or emergency conditions.
- PSM Management Program – requires an effective, written PSM program that designates the refinery manager as the person responsible for compliance, an organizational chart that identifies management responsibility for implementing PSM program elements and an assessment of process safety performance indicators against best practices, including leading and lagging factors.
Search
Recent Posts
- Navigating the One Big Beautiful Bill Act: Metallurgical Coal Added as "Critical Mineral" for Section 45X Tax Credits While Phasing out Credits for Other Applicable Critical Minerals
- President Trump’s Initiative to Simplify Federal Funding Applications
- Department of Energy Reestablishes National Coal Council
Categories
- Agreements
- Air
- Batteries
- California
- Carbon
- Carbon Markets
- CERCLA
- Chemicals
- Climate
- Coal
- Duty to Defend
- Election
- Endangered Species
- Energy Transition
- Enforcement
- Environmental
- Environmental Justice
- Environmental Law
- EPA
- ESG
- General
- General Liability
- Manufacturing
- Mining
- Natural Resources
- Oil & Gas
- Permitting
- PFAS
- Policy
- Renewables
- Trade Agreements
- Utilities
- Waste
- Water
Tags
- 2015 Standards
- 2018 Farm Bill
- 2020
- 2020 Presidential Election
- 2022 Scoping Plan for Achieving Carbon Neutrality
- 316(b)
- 3D Printer
- 3D Printing
- 4(d) Rule
- 404
- 404 permits
- 404(g)
- 45Q
- AB 1200
- AB 2503
- AB 617
- Abeyance
- ABS
- ACE
- Acrylonitrile-Butadiene-Sytrene
- active guidance
- ADAO
- Adaptation
- Adjacent
- Administration
- Administrative Agencies
- Administrative Law
- Administrative Procedure Act
- Administrator Pruitt
- Adverse Modification
- Advertizing
- Advisory Opinions
- Affordable Clean Energy
- Aftermarket Parts
- Agency
- Agency Budget
- Agency Finance
- Agency for Toxic Substances and Disease Registry
- Agency Guidance
- Agency Interpretation
- Agent
- Agriculture Improvement Act of 2018
- Air
- Air Emissions
- Air Permit
- Air Pollution
- Air Quality
- Air Quality Implementation Plan
- Air Quality Management District
- Air Quality Management Plan
- ALARP
- Alexandria Ocasio-Cortez
- Algae
- Allco Finance Unlimited v. Klee
- Allegheny
- Alternative Energy Portfolio
- Alternative Energy Portfolio Standard
- Ambient Air
- Amendments
- America's Water Infrastructure Act
- American Bar Association
- American Jobs Plan
- AMLO
- Anadarko Petroleum
- Andrés Manuel López Obrador
- Annie Kuster
- Anthony Kennedy
- Anti-Backsliding
- Anti-terrorism
- Antibacterial
- Antitrust
- AOC
- APA
- Appropriations
- APS
- AQMP
- Aquaculture
- Arbitration
- Arctice Grayling
- Arizona
- Army Corps of Engineers
- ARPA-E
- Articles
- Artificial Island transmission project
- Asbestos
- Asbestos Disease Awareness Organization
- Assumption
- Atlantic Coast Natural Gas Pipeline
- Audubon Society
- Auer
- Auer Deference
- Auxiliary Emissions Control Devices
- BAAQMD
- Backstop Siting
- BACT
- Bag Ban
- Bald and Golden Eagle Protection Act
- Bankruptcy
- BART
- Baseload
- Batteries
- battery storage
- Bay Area Air Quality Management District
- Beauty products
- Beneficial Use
- Beneficial Use and Reuse
- Bernie Sanders
- Best Available Control Technologies
- Beto O'Rourke
- BGEPA
- Biden Administration
- Bilateral Investment Treaty
- Biological Opinion
- Bipartisan Budget Act
- BIT
- Black-Capped Vireo
- BLM
- Blue Ribbon Task Force
- BOEM
- BOP
- Boston
- Boundary
- Brand Memo
- Brent Spar
- Brett Kavanaugh
- Brownfields
- BSEE
- Budget Proposal
- Bureau of Land Management
- Bureau of Ocean Energy Management
- CAA
- CAISO
- Cal-OSHA
- CalEPA
- California
- California Air Resources Board
- California Coastal Act
- California Consumer Protection Act of 2018
- California Department of Public Health
- California Department of Toxic Substances
- California Environmental Protection Agency (CalEPA)
- California Environmental Public Health and Workers Defense Act of 2019
- California Environmental Quality Act
- California Legislature
- California Mining
- California Ocean Protection Council
- California OEHHA
- California Proposition 13
- California Proposition 65
- California Regional Water Quality Control Boards
- California State Lands Commission
- California State Water Resources Control Board
- California Superior Courts
- California Title 8
- California Water Code section 13304
- California's Safe Drinking Water and Toxic Enforcement Act
- California-China Clean Technology Partnership
- Cannabis
- Cap In Place
- Cap-and-Trade
- Capital Asset Pricing Model
- CAPP
- CARB
- Carbon Capture
- Carbon Capture and Sequestration
- Carbon Capture Demonstration Projects Program
- Carbon Capture Large-Scale Pilot Projects
- Carbon Capture Utilization and Storage
- Carbon Credits
- Carbon Dioxide
- Carbon Dioxide Removal
- Carbon Intensity
- Carbon Markets
- Carbon Nanotubes
- Carbon Utilization
- CASAC
- Categorical Exclusion
- CBD
- CBI
- CCPA
- CCPS
- CCR
- CCR Rule
- CCS
- CCS Alliance
- CCUS
- CDP
- CDR
- CECP
- CEJST
- Center for Chemical Process Safety
- Centralized Waste Treatment
- CEQ
- CEQA
- CERCLA
- Certificate of Public Convenience and Necessity
- Certification
- Certified Unified Program Agencies
- CESER
- CFATS
- CFCs
- CFE
- CGL
- Chambers USA
- Chapter 91
- Chemical Data Reporting
- Chemical Exposure
- Chemical Risk Assessment
- Chemical Safety Board
- Chemicals
- Cheryl LaFleur
- Chevron Deference
- Cheyenne River Sioux
- Chloroflourocarbons
- Chlorpyrifos
- Chrysotile Asbestos
- CIP
- Circular Economy
- CITES
- Citizen Petition
- Citizen Suit
- Civil Penalties
- Civiletti
- Claims-Made
- Class VI
- Class VI Primacy
- Class VI Underground Injection Control
- Clean Air Act
- Clean Development Mechanism
- Clean Energy
- Clean Energy Resources
- Clean Energy Standard
- Clean Hydrogen
- Clean Peak Energy Certificates
- Clean Power Plan
- Clean Water Act
- Clean Water Act Section 401
- Clean Water Act Section 404
- Cleaning Products
- Cleanup
- Climate
- Climate Change
- Climate Disclosure
- Closure by Removal
- CNTs
- CO2
- CO2 Emissions
- Coakley Order
- Coal
- Coal Ash
- Coal Ash Basins
- Coal Combustion Residuals
- Coal Leasing Moratorium
- Coal Mine Health and Safety Act
- Coal Production
- Coalition for Competitive Electricity v. Zibelman
- Coastal
- Coastal Zone Management Act
- Colorado
- Comisión Federal de Electricidad
- Commercial General Liability
- Commercial Information
- Common Law
- Community Air Protection Program
- Compliance
- Comprehensive Environmental Response Compensation and Liability Act
- concurrent-remedies doctrine
- Confidential Business Information
- Congress
- Congressional Research Service
- Congressional Review Act
- Consent Decree
- Conservation Easement
- Considerations
- Constitutional Law
- Consultation
- Consumer Data
- Consumer Product Exposure Warnings
- Consumer Products
- Consumer Products Safety Commission
- Contaminated Sites
- Contribution Threshold
- Controlled Substances Act of 1970
- Cook Inlet
- Cookware
- Cooling Water Intake Structures
- Cooperative Federalism
- COP26
- COP28
- COP28 Agreement
- Coronavirus/COVID-19
- Corporate Governance
- Corporate Social Responsibility
- Corporate Sustainability
- Corporate Sustainability Reporting Directive
- Corporate Sustainability Reporting Directive (CSRD)
- Corporate Valuation
- Corps
- Cosmetics
- Cost of regulation
- Council on Environmental Quality
- County of Maui
- COVID-19
- CPCN
- CPECs
- CPP
- CPS
- CPSC
- CPUC
- CRA
- Criminal Enforcement
- Critical Electric Infrastructure Information
- critical habitat
- Critical Habitat Designation
- Critical Infrastructure
- Critical Infrastructure Protection
- Critical Materials
- Critical Minerals
- Critical Minerals Committee
- Cross-State Air Pollution Rule
- CSA
- CSAG
- CSAPR
- CSB
- CSR
- CSR reports
- CSR Standards
- CSR- and ESG-related risks
- Cultural Resources
- CWA
- CWA Citizen Suit
- CWA section 401
- CWA Section 404
- Cyber-Related Risks
- Cybersecurity
- D&O
- D&O Insurance
- Dakota Access Pipeline
- DAPL
- DARTIC
- Data Security
- DC Circuit
- DC Circuit Court of Appeals
- DCH
- Deadline Suits
- Deadlines
- Decarbonization
- Decommissioning
- Deep-Well Injection
- Deepwater Horizon
- Defeat Devices
- Defense Costs
- Deference
- Deidre G. Duncan
- Delisting
- Democratic Debate
- DEP
- Department of Energy
- Department of Homeland Security
- Department of Justice
- Department of Labor
- Department of the Interior
- Department of Transportation
- Designations
- Development
- Device
- Diligent Prosecution
- Dioxane
- Directors & Officers
- Director’s Order
- Discharge
- Diversity and Inclusion
- DJSI
- DOD
- DOE
- DOER
- DOI
- DOJ
- DOJ ENRD
- Domestic Energy Policy
- Domestic Terrorism
- DOSH
- Dow Jones Sustainability Index
- DPR
- DPU
- Draft
- Draft EA
- Draft Environmental Assessment
- drinking water
- Drinking Water Standards
- Drought
- DTSC
- Due Diligence
- Duke Energy
- Duty to Defend
- Dynamic Scoring
- E&P Wastes
- EA
- eagle
- Eagle Take Permit
- Earth Day
- Economic Impact
- Economic Impacts
- Effluent
- Effluent Guidelines
- Effluent Limitations
- EHSS
- EIS
- EJSCREEN
- Election 2020
- Electric Ratepayers
- Electric Transmission
- Electric Vehicles
- Electricity
- Electricity Markets
- ELG
- ELGs
- Elizabeth E. Aldridge
- Elizabeth Warren
- Emergency Planning and Community Right-to-Know Act
- Emergency Response
- Emergency Support Functions
- Emerging Contaminants
- Emission Caps
- Emission Control Requirements
- Emission Reduction Credits
- Emissions
- Emissions Caps
- emissions reporting
- Emphasis List
- Endangered Species
- Endangered Species Act
- Energy
- Energy Industry
- Energy Infrastructure
- Energy Package Insurance
- Energy Reforms
- Energy Storage
- Energy Transition
- Enforcement
- Enforcement Discretion
- Enforcement statistics
- Engine Certification
- Enhanced Oil Recovery
- ENRD
- Environment
- Environment and Natural Resources Division
- Environmental
- Environmental and Social Governance
- Environmental Appeals Board
- Environmental Assessment
- Environmental Bar
- Environmental Compliance
- Environmental Crimes
- Environmental Defense Fund
- Environmental Disclosure
- Environmental Due Diligence
- Environmental Enforcement
- Environmental Groups
- Environmental Impact Statement
- Environmental Justice
- Environmental Justice and Equity Board
- Environmental Law
- Environmental Law Institute
- Environmental Markets
- Environmental Permitting
- Environmental Protection Agency
- Environmental Protection Agency (EPA)
- Environmental Rights
- Environmental Social and Corporate Governance
- Environmental Social and Governance
- Environmental Social Governance
- Environmental Social Justice
- Environmental Transactions
- EO 13891
- EOR
- EP3
- EP4
- EPA
- EPA audit policy
- EPR
- EPR Laws
- Equator Principles
- Equator Principles Association
- ERC
- ESA
- ESA consultation
- ESA section 7 consultation
- ESG
- ESG Diligence
- ETP
- EU
- European Climate Law
- European Green Deal
- European Sustainability Reporting Standards
- European Union
- Evaluation of Regionalization for Potential New Wastewater Systems
- EVs
- Exceptional Events
- Exceptional Events Rule
- Excess Insurance
- Excess Liability
- Exchange Act
- Executive Compensation
- Executive Memorandum
- Executive Office for United States Attorneys
- Executive Order
- Executive Order 13777
- Executive Order 14008
- Executive Order N-8-23
- Executive Orders
- Extended producer Responsibility
- Extended Producer Responsibility (EPR)
- Fair and Equitable Treatment
- Fair Labor Standards Act
- FAR
- FAST Act
- FAST-41
- Fathead Minnow
- Fatmucket Mussel
- FDA
- FECM
- Federal Acquisition Regulations
- Federal Action
- Federal Agencies
- Federal Agency Action
- Federal Budget
- Federal Energy Regulatory Commission
- Federal Lands
- Federal Permit
- Federal Power Act
- Federal Preemption
- Federal Register
- Federal Rule 20
- Federal Rule 71.1
- Federalism
- Fees
- FERC
- FET
- Fiduciary Liability
- FIFRA
- Fifth Circuit
- Final Rule
- Financial Information
- Fireworks
- First Amendment
- Fishing Industry
- Flaring
- Flint
- FloaTEC LLC
- Flood Infrastructure Funding
- Flood Mitigation
- Florida
- FLSA
- FOIA
- Food
- Food and Drug Administration
- Food and Drug Administration (FDA)
- Food Loss and Waste
- Food Marketing Institute
- Food Marketing Institute v. Argus Leader Media
- Food Waste
- Food Waste Reduction Alliance
- Fossil Fuels
- Fourth Circuit
- Fourth of July
- FPA
- FPA Preemption
- FPA section 202(c)
- FPOS
- Fracking
- Framework
- Framework Rule
- Fraud
- Free Trade Agreement
- Freedom of Information Act
- Freeport
- FSLA
- FTA
- Funding for Environmental Protection
- Funding Mechanism
- FUTURE Act
- FWS
- FY2017 budget
- FY2018
- GAO
- Gas
- GDPR
- Gender Equality
- General Data Protection Regulation
- General Industrial Stormwater Permit
- General Permit
- GenX
- George Clemon Freeman Jr.
- GHG
- GHG Emissions
- GHG Emissions Renewable Portfolio Standard
- Gilbert & Sullivan
- Global Carbon Markets
- Global Climate Negotiations
- Global Reporting Initiative
- Global Warming Solutions Act
- Glyphosate
- GOM
- Good Neighbor Obligation
- Good Neighbor Provision
- Government Investigations
- Grand River Dam Authority
- Grassroots Activisim
- Green Admendment
- Green Communities Act
- Green Deal
- Green New Deal
- Green New Deal; Climate Change
- Greenhouse Gas
- Greenhouse Gas Emissions
- Greenhouse Gas Protocol
- Greenhouse Gas Protocol Initiative
- Greenhouse Gases
- Grid
- grid reliability
- grid study
- Grocery Manufacturers Association
- Groundwater
- Guam
- Guidance
- Guidance Portal
- Gulf of Mexico
- Habitat
- Hardrock Mining Rule
- Harmful Algal Blooms
- Hawaii
- Hawkes
- Hazardous Air Pollutants
- Hazardous Materials Regulations
- Hazardous Waste
- HBCD
- HCFCs
- Health
- Health Advisories
- Health Advisory
- Health and Safety
- HECT
- Hemp
- HFCs
- High-Density Polyethylene (HDPE)
- Highly Reactive Volatile Organic Compound Emissions Cap and Trade
- Historical Matter
- HMR
- Holder
- Homeland Security
- Hoopa Valley Tribe
- House
- House of Representatives
- Houston Casualty
- Human Health Toxicity Values
- Human Rights
- Hurricane Harvey
- Hydraulic Fracturing
- Hydroelectric Relicensing
- Hydrofluorocarbons
- Hydrofluorocarbons (HFCs)
- Hydrogen
- Hydrogen Energy Earthshot
- Hydrological Connection Theory
- Hydropower
- ICMM
- ICSID
- IFC Performance Standards
- IGP
- IIA
- IIJA
- Impaired Waterbodies
- Impaired Waters
- Impairment
- Incident Response
- Incidental Take
- incidental take statement
- Indian Lands
- Indigenous Traditional Ecological Knowledge
- Indonesia
- Industrial Accidents
- Industrial Hemp
- Infectious Disease Preparedness and Response Plan
- Inflaction Reduction Act
- Infrastructure
- Infrastructure Development
- Infrastructure Investment and Jobs Act (IIJA)
- infrastructure security
- Initial & Boundary
- Innovation
- Inside Look
- Inspections
- Insurance
- Insurance Recovery
- Integrated Science Assessment
- Interagency Review
- Intergovernmental Panel on Climate Change
- Interior
- International Arbitration
- International Centre for Settlement of Investment Disputes
- International Council on Mining and Metals
- International Energy Agency
- International Environmental Law
- International Investment Agreements
- International Petroleum Industry Environmental Conservation Association
- Interstate Transport
- Intervention
- Investment Risk Assessment
- IPCC
- IRIS
- IRIS Review
- IRS
- ISO-NE
- ITEK
- Jay Inslee
- Jewell
- Joe Biden
- John Hickenlooper
- Joint Venture Provision
- Judicial Review
- Judiciary
- Jurisdiction
- Jurisdictional Determination
- Justice40
- Kamala Harris
- Kavanaugh
- Kenk’s amphipod
- Kevin McIntyre
- Keystone XL
- Kigali Amendment
- Kisor
- Kisor Deference
- Kyoto Protocol
- Lake Erie
- Lake Powell Pipeline Project
- Lampsilis Siliquoidea
- Land Use
- Late Notice
- Lautenberg Act
- Law360
- LCPFAC SNUR
- LDC
- LDNR
- Lead
- Lead and Copper Rule
- Lease Sale
- Legislation
- Lesser Prairie Chicken
- Li-ion
- Liability
- Liability Insured
- Linear
- Liquefied Natural Gas
- Lithium-ion batteries
- Litigation
- Lloyds
- Lloyd’s of London
- LNG
- London Protocol
- Long-Form Warning
- Look-back period
- Louisiana Department of Natural Resources
- Low Carbon Fuel Standard
- MA DOER
- Maine
- Maine Department of Environmental Protection
- Maintenance Fees
- Malaysia
- Manufactured Products
- Manufacturers
- Manufacturing
- Marijuana
- Maritime
- Markets
- Masias
- Mass Emissions Cap and Trade
- Massachusetts
- Massachusetts AG
- Massachusetts Clean Energy Center
- Massachusetts Climate Act
- Massachusetts Department of Energy Resources
- Massachusetts Global Warming Solutions Act
- MassCEC
- MATS
- Maximum Contaminant Levels
- MBTA
- MBTA; Wind Energy; Renewable Energy; protected species; natural resources; USFWS
- McGraw-Edison
- McIntyre
- MCL
- MCLG
- MCLs
- McNamee
- MEA
- MECT
- Mergers & Acquisitions
- Methane
- methane emissions
- Methane Repeal Rule
- Methylene Chloride
- Michigan
- microplastics
- Midnight Rule
- Midstream
- Migratory Bird Treaty Act
- Migratory Birds Treaty Act
- Millennium Pipeline
- Mineral Law of 1872
- Mineral Leasing Act
- Mineral Policy
- Mining
- Mining Claims
- Minnesota
- Minnesota Pollution Control Agency (MPCA)
- Misbranding
- Mitigation
- Mitigation Rule
- MLP
- Modification
- Monitoring
- Monsanto
- Montana
- Montreal Protocol
- Moratorium
- MOU
- Mountain Valley Pipeline
- MSGP
- Multi-Sector General Permit
- Multiyear Plan for Energy Sector Cybersecurity
- Mulvaney
- Murray
- Murray Energy
- MVP
- NAAQS
- NAFTA
- NAIOP
- NALs
- Nancy Pelosi
- NATA
- National Ambient Air Quality Standards
- National Compliance Initiatives
- National Cybersecurity and Communications Integration Center
- National Defense Authorization Act
- National Determined Contributions
- National Emergency
- National Enforcement and Compliance Initiatives
- National Enforcement Initiatives
- National Environmental Policy Act
- National Historic Preservation Act
- National Hydro Association
- National Marine Fisheries Service
- National Oceanic Atmospheric Administration
- National Parks and Conservation Ass’n v. Morton
- National Petroleum Council
- National Pollutant Discharge Elimination System
- National Pollutant Discharge Elimination System (NPDES)
- National Pollution Discharge Elimination System
- National Primary Drinking Water Regulation
- National Priorities List
- National Recycling Strategy
- National Register of Historic Places
- National Restaurant Association
- National Security
- Nationwide Permit
- Native American Law
- Natural Gas
- Natural Gas Act
- Natural Gas Leak Abatement Program
- Natural Gas Pipeline Certification
- Natural Gas Pipelines
- Natural Resource Damages
- Natural Resources
- Navigable waters
- NCCIC
- NCI
- NEC
- NECIs
- NEI
- Neil Chatterjee
- NELs
- NEPA
- NEPA Policy
- NEPA Review
- NERC
- NESCOE
- Net-Zero Emissions
- Net-Zero Greenhouse Gas Emissions
- New Chemicals Review Program
- New Rule
- New Source Review
- New York
- New York Department of Environmental Conservation
- New York State Department of Taxation and Finance
- NGA
- NGO
- NHPA
- NHTSA
- NIETC
- nitrogen dioxide
- NMFS
- No Exposure Certification Identification Number
- No-Action Letter
- NOAA
- NOI
- NONA
- Nonapplicability Identification Number
- Nonattainment
- Nonpoint Source
- North American Electric Reliability Corporation
- North Dakota
- Notice
- Notice of Proposed Rulemaking
- NPDES
- NPDES Delegation
- NPDWR
- NPL
- NSPS
- NSR
- Nuclear
- Nuclear Energy
- NWP
- NY PSC
- Obama
- Occupational Safety and Health Act
- Occupational Safety and Health Administration
- OCE
- OECA
- OEHHA
- OEJECR
- Office of Civil Enforcement
- Office of Cybersecurity Energy Security and Emergency Response
- Office of Electricity Delivery & Energy Reliability
- Office of Enforcement and Compliance Assurance
- Office of Enforcement and Compliance Assurance (OECA)
- Office of Environmental Justice and External Civil Rights
- Office of Federal Register
- Office of Information and Regulatory Affairs
- Office of Management and Budget
- Office of Natural Resources
- Office of Water
- Offshore Energy
- Offshore Platforms
- Offshore Wind
- Offshore wind energy
- Ohio
- Oil
- Oil & Gas
- Oil and Gas
- Oil and Gas Production
- Oil and Gas Wastewater
- Oil Pipelines
- Oil Pollution Act
- OIRA
- Oklahoma
- OMB
- One Federal Decision
- One Federal Plan
- OPA
- Oregon
- OSHA
- Outer Continental Shelf
- OW
- Ozone
- Pacific OCS Region
- Packaging
- Paperwork Reduction Act
- Paris Agreement
- Paris Climate Accord
- Paris Climate Agreement
- Particulate Matter
- Partido Revolucionario Institucional
- Passaic River
- PATH Act
- PBT
- PCBs
- PEMEX
- Penalties
- Penalty
- PennEast Pipeline
- Pennsylvania
- Perfluoroalkyl
- Permian Basin
- Permitting
- Pesticide Devices
- Pesticides
- Pete Buttigieg
- Petition
- Petition for Rulemaking
- Petitions for Objection
- PetraNova
- Petrochemical Regulation
- Petróleos Mexicanos
- Petroleum Products
- PFAS
- PFAS Action Plan
- PFAS in Products State Law Tracker
- PFAS Reporting Rule
- PFAS Strategic Roadmap
- PFBA
- PFBS
- PFNA
- PFOA
- PFOS
- PHMSA
- Physicians for Social Responsibility
- Pimphales Promelas
- PIP
- Pipe Manufacturing
- Pipeline
- Pipeline and Hazardous Materials Safety Administration
- Pipeline Attacks
- Pipeline Construction
- Pipeline Safety
- Pipelines
- PIPES
- Plastic
- Plastic Carryout bag
- PNAS
- POCSR
- Point Source
- Point Source Discharge
- Policy
- Policy Statement
- Pollution
- Pollution Exclusion
- Pollution Liability
- Pollution Prevention for Healthy People and Puget Sound Act
- Polyalkyl
- Polyfluoroalkyl
- Port of Los Angeles
- Porter-Cologne Water Quality Control Act
- Potentially Responsible Party
- POTW
- PRA
- Practical Law
- Precedent
- Preconstruction Authorizations
- Preemption
- Prejudice
- Preliminary Injunction
- President Biden
- President Trump
- Presidential Transition
- PRGs
- PRI
- Priebus
- Principal
- Principles for Responsible Investments
- Priority Pollutants
- Privacy
- Process Safety Management
- Produced Water
- Product Safety
- Production Cuts
- Production Sharing Contract
- Prohibition on Sale
- Project Development
- Prop. 65
- Proposition 65
- Protected Species
- Protecting Our Conserved Lands Act of 2019
- PRP
- Pruitt
- Pruitt Task Force
- PSC
- PSD
- PSH
- PSM
- Public Comment
- Public Lands
- Public Utilities
- Publicly Owned Treatment Works
- Pumped Storage Hydropower
- PURPA
- Quality Assurance Plan
- R-Project Transmission Line
- Racing Vehicles
- RAGAGEP
- Railroad Commission
- Railroad Commission of Texas
- Railroad Commission of Texas (RRC)
- Rapanos
- RBI
- RCRA
- RCRA Subtitle D
- REACH
- Reasonable Progress Plans
- RECLAIM
- Reconsideration
- RECs
- Redevelopment
- Refinery
- Reform
- Reforma Energética
- Regional Clean Air Incentives Market
- Regional Clean Hydrogen Hubs
- Regional Greenhouse Gas Initiative (RGGI)
- Regional Haze
- Regional Water Quality Control Boards
- Registration Evaluation Authorization and Restriction of Chemicals
- Regulation
- Regulation S-K
- Regulation S-X
- Regulations
- Regulatory
- Regulatory Agenda
- Regulatory Freeze
- Regulatory Guidance
- Regulatory Programs
- Regulatory Reform
- Regulatory Review
- Reliability
- Reliability Safety Valve
- Remediation
- Removal Action
- Renewable
- Renewable Energy
- Renewable Energy Certificates
- Renewable Energy Portfolio
- Renewable Fuel Standards
- Renewable Portfolio Standard
- Renewables
- Renewals
- Reporting
- Request for Information
- ReRED
- Rescind
- Resilience of the Bulk Power System
- Resource Conservation and Recovery Act
- Responsible Business Initiative
- Restoration
- Restriction of Hazardous Substances
- Retail
- Retailers
- Retained
- Retroactivity
- Return on Equity
- RFS
- RHA
- Richard Glick
- Rigs to Reefs
- RIN
- Ripeness
- Risk and Technology Review
- Risk Assessment
- Risk Evaluation
- Risk Management
- Risk Management Plan
- Risk Management Program
- Risk Management Regulations
- Rivers and Harbors Act
- RMP
- Roadmap Release
- Roanoke River Basin Association
- Robert Powelson
- ROE
- ROEs
- RoHS
- Roundtable on Sustainable Palm Oil
- Roundup
- Royalties
- RPS
- RRBA
- RRC
- RTR
- Rule 14a-8(i)(7)
- Rule 65(c)
- Rulemaking
- Russia
- SAB
- Sackett
- Sacred Sites
- SAFE
- Safe Drinking Water Act
- Safe Harbor
- Safe Harbor Regulation
- Safe Harbor Warning
- Safer Consumer Products
- SAFETY Act
- Safety Management System
- San Francisco Bay Regional Water Quality Control Board
- SASB
- SaskPower’s Boundary Dam Unit 3
- SB 1371
- SCAQMD
- Science
- Science Advisory Board
- Science Advisory Board (SAB)
- Scope
- Scope 1
- Scope 2
- Scope 3
- Scott Pruitt
- SCOTUS
- SDWA
- SEC
- Section 10
- Section 104 Request
- Section 114 Request
- Section 179B(b)
- Section 208 Request
- Section 308 Request
- Section 4
- Section 401
- Section 404
- Section 408
- Section 45Q
- Section 5
- Section 6(b)
- Securities Act
- Securities and Exchange Commission
- Securities and Exchange Commission (SEC)
- Securities Law
- Seismicity
- Seminole Rock
- Senate
- Senate Energy and Natural Resources Committee
- Senator Lamar Alexander
- SEP
- SEPs
- Services
- Settlements
- Sewage
- Shareholder Lawsuits
- Shutdown
- Sierra Club
- Significant Figures
- Significant Guidance
- Significant New Use Rule
- SIP
- Smelter
- SNUR
- Social
- Social Media
- Solar
- Solid Waste
- South China Sea
- South Coast Air Quality Management District
- SPCC
- Species
- Spill Prevention Control and Countermeasure Rule
- SSB 5135
- SSM SIP Call
- Stabilization Clause
- Standing
- Standing Rock Sioux
- Stare Decisis
- State
- State Administrative Appeals
- State Air Pollution Control Board
- State Constitutions
- State Environmental Quality Review Act
- State Implementation Plan
- State Law
- State Water Resources Control Board
- States
- Statute of Limitations
- Statutory Authority
- Statutory Interpretation
- Stormwater
- Strategic
- Straw Proposal
- Subrogation
- sulfur dioxide
- Sunset Review
- Superfund
- Supplemental Environmental Projects
- Supply Chain
- Supreme Court
- Supreme Court of Texas
- Supreme Court of the United States
- Surface Mining Act
- Surface Mining and Reclamation Act
- Surface Water Discharge
- Susan Bodine
- Sustainability
- Sustainability Accounting Standards Board
- Sustainable Development Goals
- Sustainable Investing
- SWDA
- Switzerland
- SWRCB
- Tailings Storage Facility
- Take
- Take Prohibition
- Takings
- Task Force on Climate-Related Financial Disclosures (TCFD)
- Tax
- Tax Credit
- Tax Credits
- Tax Cuts and Jobs Act
- Tax Reform
- Taxonomy Regulation
- TCEQ
- TCI
- Temporary Policy
- TERP
- Texas
- Texas Alliance of Energy Producers
- Texas Commission on Environmental Quality
- Texas Legislature
- Texas Railroad Commission
- Texas Water Development Board
- Thailand
- THC
- The European Commission
- The Mikado
- The Treasury Department
- The Water Infrastructure Improvements Act
- the WIIN Act
- Third Circuit
- Threatened Species
- Title V
- TMDL
- TMDLs
- TNALs
- Toledo
- Tolling Order
- Total Maximum Daily Load
- Toxic Chemicals
- Toxic Substances Control Act
- Toxic Substances Control Act (TSCA)
- Toxics
- Toxics Release Inventory
- Transcos
- Transition
- Transmission
- Transparency
- Transport
- Treasury
- Treaty Rights
- Trends
- TRI
- Tribal Rights
- Tribes
- Trump
- Trump Administration
- TSA
- TSCA
- TSF
- TWDB
- U.S. Army Corps of Engineers
- U.S. Environmental Protection Agency
- Ultimate Net Loss
- UNCLOS
- Underground Injection Wells
- Underground Storage Tank
- UNFCCC
- Unified Agenda
- United Airlines
- United Nations
- United Nations Framework Convention on Climate Change
- Urgenda
- US Army Corps of Engineers
- US Chemical Safety Board
- US Climate Alliance
- US Court of Appeals for the Ninth Circuit
- US Customs and Border Protection
- US Department of Agriculture
- US Department of Justice (DOJ)
- US Environmental Protection Agency
- US Fish and Wildlife Service
- US FWS
- US SAFETY Act
- US Securities and Exchange Commission
- US Securities and Exchange Commission (SEC)
- US Supreme Court
- USACE
- USDA
- USDOT
- USFWS
- USMCA
- Utilities
- Utility
- Vapor Intrusion
- Vapor Recovery Units
- VCP
- Venting
- Veto
- Village of Old Mill Creek. v. Star
- Vineyard Wind
- Virginia Clean Economy Act
- Virginia Community Flood Preparedness Fund
- Virginia Department of Environmental Quality
- Virginia State Corporation Commission
- Vision of Corporation Finance
- VOCs
- Volatile Organic Compounds
- Voluntary Cleanup Program
- Voluntary Remediation
- Waiver
- Waiver Period
- Warnings
- Washington
- Waste
- Waste Discharge Identification Number
- Waste Electrical and Electric Equipment
- Waste Permitting
- Wasted Food
- Wastewater
- Wastewater Treatment
- Water
- Water Quality Certification
- Water Quality Criteria
- Water Regulation
- Water Reuse
- Water Supply and Management
- Water Systems
- Waterfront
- Waters
- Waters of the United States
- WDID
- WEA
- WEEE
- Well Blowout
- Well Control Rule
- WET Tests
- Wetlands
- Whole Effluent Testing
- Wholesale Electricity
- WildEarth Guardians
- Wildfire
- Wind
- Wind Energy
- Wind Energy Area
- Wind Farms
- Winning on Reducing Food Waste Initiative
- Winter v. NRDC
- Withdrawal or Reinstatement
- World Bank Group Equator Principles
- Worst-Case Discharge
- WOTUS
- WQBELs
- WQC
- Wyoming
- Zero Emissions
- Zero-Emissions Vehicle Initiative
- Zinke
Authors
- Yaniel Abreu
- Walter J. Andrews
- Fatima Anjum
- John J. Beardsworth, Jr.
- Jordan L. Bernstein
- Timothy E. Biller
- John R. Bobka
- George Borovas
- Lawrence J. Bracken II
- Shannon S. Broome
- Karma B. Brown
- Samuel L. Brown
- F. William Brownell
- Courtney Cochran Butler
- Michelle G. Chan
- E. Carter Chandler Clements
- Abigail Contreras
- Benjamin Y. Cooper IV
- Eric S. Crusius
- Christopher J. Cunio
- Alexandra B. Cunningham
- Field Daniel
- Andrea DeField
- Meredith Doswell
- Douglas L. Dua
- Deidre G. Duncan
- Frederick R. Eames
- Kevin S. Elliker
- Clare Ellis
- Latosha M. Ellis
- Joanna D. Enns
- Susan S. Failla
- Geoffrey B. Fehling
- Andrea Field
- Hannah Flint
- Steven C. Friend
- Kevin E. Gaunt
- Andrew G. Geyer
- David N. Goldman
- Elisabeth R. Gunther
- Steven M. Haas
- Alexandra Hamilton
- James W. Head
- Patrick Jamieson
- Kevin W. Jones
- Laura Ellen Jones
- Dan J. Jordanger
- Ryan T. Ketchum
- Sami M. Khan
- Jonathan H. Kim
- Scott H. Kimpel
- Charles H. Knauss
- J. Pierce Lamberson
- Lucinda Minton Langworthy
- Matthew Z. Leopold
- Charlotte Leszinske
- Brian R. Levey
- Michael S. Levine
- Elbert Lin
- Eric R. Link
- Nash E. Long
- David S. Lowman, Jr.
- James Martin
- Jeffrey N. Martin
- Lorelie S. Masters
- Patrick M. McDermott
- Kerry L. McGrath
- Robert J. McNamara
- Nathan R. Menard
- Michael J. Messonnier, Jr.
- Jennifer MikoLevine
- Todd S. Mikolop
- Angela Morrison
- Michael J. Mueller
- Eric J. Murdock
- Ted J. Murphy
- William L. Newton
- Paul T. Nyffeler, PhD
- Peter K. O’Brien
- G. Michael O’Leary
- Evangeline C. Paschal
- Kate Perkins
- Shemin V. Proctor
- Shawn Patrick Regan
- Myles F. Reynolds
- Doris Rodríguez
- Brent A. Rosser
- Rachel Saltzman
- Arthur E. Schmalz
- Penny A. Shamblin
- Michael R. Shebelskie
- George P. Sibley, III
- Joseph C. Stanko
- Martin P. Stratte
- Javaneh S. Tarter
- Thomas W. Taylor
- David Arthur Terry
- Patricia Tiller
- Linda Trees
- Andrew J. Turner
- Emily Burkhardt Vicente
- Ayesha K. Waheed
- Gregory R. Wall
- Daniel C. Warren
- Thomas R. Waskom
- Malcolm C. Weiss
- Susan F. Wiltsie